… celem optymalizacji procesu produkcyjnego
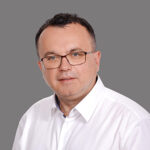
Płytki bezpieczeństwa stosowane są do zabezpieczenia instalacji oraz urządzeń przed nadmiernym wzrostem ciśnienia lub przed jego spadkiem (próżnią). Używane są do zabezpieczenia instalacji procesowych, autoklawów, bioreaktorów, wymienników ciepła, fermentorów, zbiorników magazynowych, urządzeń mieszających czy suszących.
Płytki bezpieczeństwa mogą być używane jako jedyne, podstawowe zabezpieczenie instalacji lub jako drugie zabezpieczenie wraz z zaworem bezpieczeństwa lub jako kombinacja w układzie płytka bezpieczeństwa montowana pod zaworem bezpieczeństwa. Zaletą działania płytki bezpieczeństwa jest jej rozerwanie i zadziałanie w milisekundach, przy osiągnięciu żądanego ciśnienia rozerwania. Jest to więc najbardziej pewne, mechaniczne zabezpieczenie instalacji.
Pierwszym krokiem optymalizacji procesu produkcji jest więc wybór tylko płytki bezpieczeństwa jako jedynego zabezpieczenia przed próżnią lub przed wzrostem ciśnienia. W zależności od wartość „OR”, czyli ciśnienia roboczego do minimalnej wartości ciśnienia rozerwania oraz charakteru pracy instalacji czy urządzenia, możemy wybrać płytki wklęsłe lub płytki wypukłe. Odpowiednio przedstawione są na rysunkach 1 i 2.
Jeśli więc wartość OR jest większa niż 80%, możemy wybrać płytki odwróconego działania (płytki wypukłe). Tego typu płytki rekomendowane są do pracy przy ciśnieniu roboczym wynoszącym aż 95% minimalnego ciśnienia rozerwania oraz w przypadku wystąpienia próżni. Płytki typ SANITRX HPX (II) 95 produkcji Continental Disc Corporation spełniają te wymagania.
Prawidłowy dobór
Pomijając dobór wymiarów płytki z uwagi na jej przepustowość, drugim krokiem optymalizacji jest więc prawidłowy dobór ciśnienia jej rozerwania. Ciśnienie rozerwania, zgodnie z normą ISO 4126-6, definiowane jest jako wartość rozerwania płytki znajdująca się pomiędzy jej maksymalną wartością ciśnienia rozerwania a minimalną wartością ciśnienia rozerwania. Maksymalne (MBR), jak i minimalne ciśnienie rozerwania (MNBR) musi zostać określone przez producenta w zależności od temperatury procesu i wykonania materiałowego płytki. Pomiędzy tymi wartościami jest tzw. Performance Tolerance (tolerancja zadziałania), która dla płytek odwróconego działania typ SANITRX HPX wynosi tylko +- 5%. W tabeli 2 normy ISO 4126-6 podane są typowe, standardowe wartości tolerancji zadziałania. Każda podana wartość w tabeli obciążona jest jeszcze tzw. tolerancją wykonania producenta, w przypadku płytek SANITRX HPX wartość ta wynosi 0%. Oznacza to, że jeśli na tabliczce znamionowej, zgodnie z wymogami PED oraz normy ISO 4126, podane są wartości max/min ciśnienia ro- zerwania, to nie są one obarczone żadnym błędem, dodatkową tolerancją wykonania. Jeśli na instalacji występuje pulsacyjne ciśnienie robocze, najwyższe jego wartości nie mogą jednak przekroczyć minimalnego ciśnienia rozerwania, płytka przy tym ciśnieniu może, ale nie musi ulec rozerwaniu.
Korzystniejszym rozwiązaniem z punktu widzenia optymalizacji procesu produkcji byłoby więc użycie tylko płytki zrywnej. Sprężynowy zawór bezpieczeństwa będzie bowiem pracował niestabilnie, będzie się lekko otwierał i natychmiast zamykał upuszczając ciśnienie. Na skutek niecałkowitego otwarcia zaworu wypływające medium z pewnością spowoduje erozję krawędzi gniazda zaworu. (Sprężynowe zawory bezpieczeństwa ustawiane są z tolerancją +- 3% ciśnienia nastawy). Może dojść do uszkodzenia gniazda zaworu i jego grzybka.
Trzecim krokiem optymalizacji produkcji jest oszczędność zabudowy na instalacji. Płytki monto- wane są na rurociągu, w holderach lub w mocowaniu zaciskowym.
Zajmują bardzo mało miejsca, dodatkowo ta- bliczka znamionowa może być odpowiednio zagięta, co ułatwiała bezpieczne przejścia oraz dostęp do urządzenia. Wszystkie płytki produkowane przez Continental Disc Corporation rozrywają się bez defragmentacji dysku, co oznacza, że żadne jego fragmenty nie znajdą się w instalacji. Można więc płytki montować w dowolnym miejscu procesu, oczywiście tak, aby spełniały swoją funkcję. Koszty prowadzenia procesu związane są również z kosztami części zamiennych lub konserwacji. Płytki bezpieczeństwa nie wymagają konserwacji, obsługi, okresowych przeglądów czy części zamiennych.
Czwartym krokiem optymalizacji procesu jest montaż czujnika rozerwania płytki.
CDC zapewnia dwa systemy: BDI sensor system oraz BDI alarm system. Oba te systemy mogą być podłą- czone bezpośrednio do głównego systemu sterowania zakładu, informując natychmiast obsługę o rozerwaniu płytki, a tym samym o konieczności zatrzymania procesu. Natychmiastowe zamknięcie procesu wpłynie na oszczędności zużycia danego medium.
Literatura
- Norma ISO 4126-6.
- Materiały techniczne Continental Disc Corporation.
Czy chciałbyś więcej dowiedzieć się o tym produkcie albo przedyskutować przyszły projekt? Proszę skontaktuj się, ze specjalistą Thurne.
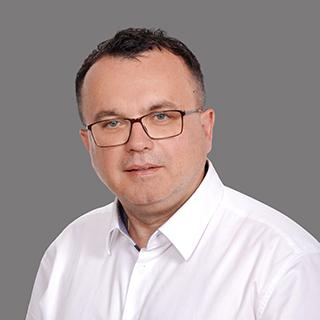